Køkkenproducent har taget digitalt tigerspring og minimeret servicetiden
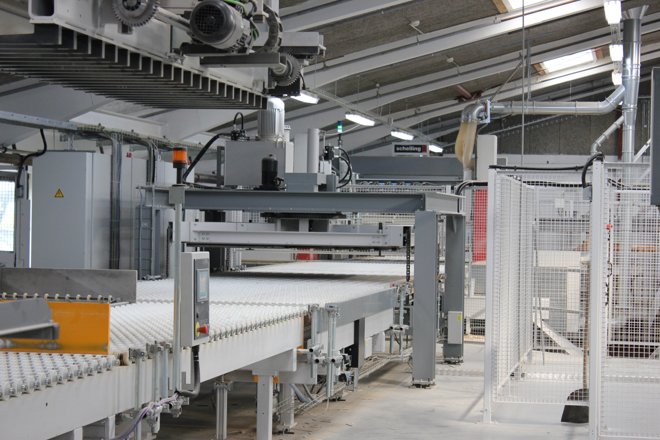
I de seneste år har Kvik tillige med resten af landets køkkenproducenter oplevet en massiv efterspørgsel. For at kunne følge med og i samme ombæring reducere CO2-udledningen fra produktionen i Vildbjerg har Kvik investeret massivt i maskiner og teknologi i de seneste år, og her er en løsning til indsamling af data i produktionen seneste skud på stammen.
For et halvt år siden implementerede Kvik nemlig en cloudbaseret softwareløsning – Opticloud – fra OptiPeople, som foreløbigt er koblet på seks ud af tolv anlæg, og nye målinger viser, at Kvik allerede nu ser gevinster ved brug af løsningen.
– Vi arbejder hele tiden på at optimere vores produktion, og derfor indledte vi samarbejdet med OptiPeople, da vi gerne ville have mere præcise og valide data fra vores anlæg. Først og fremmest for at få et mere præcist indblik i årsagerne til stop. Dernæst for at bruge de data til at planlægge en bedre proces for vedligehold af maskinerne for således at minimere den tid, hvor en maskine ikke producerer, fortæller Stefan Lindell, som er LEAN Project Manager hos Kvik.
Løsningen har nu været benyttet i et halvt år, og derfor var det altså på tide at måle de foreløbige resultater.
– I en måned målte vi af den grund på stop og produktionstid på anlæggene, og her kan vi se, at vi på relativt kort tid allerede har cirka 50 procent færre servicetimer på vores maskiner med 1-holdskift eller færre skift, mens vi på maskiner med 3-holdsskift har formået at minimere service med omtrent 40 timer om året, hvilket giver 40 timers ekstra produktion, fortæller Stefan Lindell.
En løsning med flere muligheder
Helt konkret er Kvik lykkedes med at skabe resultaterne ved blandt andet at skifte fra at udføre service ud fra et fast tidsinterval til nu at gøre det efter et specifikt antal produktionstimer. Og ifølge CEO hos OptiPeople, Stefan Jensen, er det et greb, som mange produktionsvirksomheder vil kunne se en gevinst ved.
– Kvik har sat ind på flere fronter for at optimere driften på produktions- og pakkeanlæggene, og her er en af hovedpunkterne, at de er gået over til nu at udføre service, når en maskine har kørt et bestemt antal timer – fremfor blot at gøre det efter en vis rum tid, siger han.
– Vi ser mange virksomheder, der enten ikke udfører forebyggende vedligehold og således bare venter på, at der sker nedbrud, eller som baserer det på tid. Men når man som hos Kvik har maskiner, der ikke kører hele tiden og andre, som kører mere end forventet, giver det ikke mening at basere service på tidsintervaller – i så fald risikerer man at have et anlæg til at stå stille, og det er jo både dyrt og uhensigtsmæssigt, hvis man samtidig er udfordret af en stor efterspørgselm lyder det videre.
Hos Kvik er det stadig nyt at bruge Opticloud, og ifølge Stefan Lindell rummer løsningen således et stort potentiale – blandt andet også for at indsamle data som grundlag for investeringer og for at reducere CO2-udledningen fra produktionen.
– Det tager tid at køre ny teknologi ind i en produktion, og vi har for eksempel stadig seks anlæg, der skal kobles på løsningen. På den længere bane ser vi udover optimering af driften også muligheder i at bruge data fra de enkelte maskiner til at træffe beslutninger om at investere i nyt udstyr, mens vi ikke mindst også gerne vil bruge Opticloud til at registrere energiforbrug, som vi kan bruge i vores bæredygtighedsarbejde, siger han.